Security system installations are rarely done in a vacuum, although many integrators would tell you otherwise. Often the emphasis is on getting in and out quickly — after all, time is money, right?
Unfortunately, as many learn the hard way, that axiom cuts both ways. Sure, it’s more profitable to complete a job quickly than to see it drag out, but repeated returns to the job site to resolve problems that could have been handled right in the first place cost dearly, in time, profitability, and — perhaps most importantly — customer satisfaction.
Some common areas where an ounce of prevention is worth a pound of cure:
Permits and licenses
This one has been a big one for our firm lately. It seems that many integrators only want to get the required permits and inspections when they are caught in the act. It is far easier to comply with the law than get caught breaking it and having to make amends. Permits and inspections are there to assure that the work was done properly and to code, and if you’re doing your job properly they should be no issue. We’ve seen integrators have to completely redo work because an electrical inspector was unhappy with the electrical panel being used, and subcontracted electrical work doesn’t usually come cheap.
Labeling
You may not want to label all outlets and circuit breakers that feed security equipment, but why not? After all, with a glass of water and a can of spray paint, almost any security equipment can be disabled if you have access to the equipment closet. The danger is far more likely to come from an accidental unplugging, and that is easily prevented by a neat, professional looking “CAUTION: DO NOT UNPLUG” sign.
Territory review
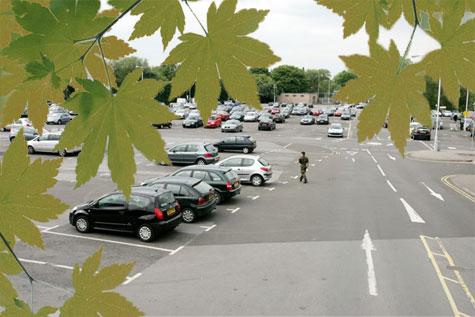
Make sure the system isn’t encroaching on someone else’s territory. If you install a camera in the summer and you find out later that the Christmas decorations will block the view five months later, I’ll wager the camera will wind up getting moved before the Christmas decorations. We’ve seen equipment plugged into outlets that may be periodically turned off, cameras blocked by spring foliage that was missed during a winter installation, and other preventable obstacles.
Training
This should be more than a five-minute “here’s how it works” session. More than one person should be familiarized with their system, no matter how small, and training should be conducted in conjunction with “leave behind” material. This allows them to look things up themselves later, rather than call you, or complain the system doesn’t work right. It may be crude, but consider leaving a copy of the operation manual in the bathroom — sooner or later, someone will read it!
Scheduled maintenance
If there are things that need to be done to maintain the system, ensure that they are pointed out if you’re not ultimately going to be handling things. Cleaning filters and lower domes on cameras can often be handled by an end-user if they’re told about it, or bringing it up may lead to a contract for preventive maintenance. But, if left to slowly degrade performance, you’ll ultimately get the blame if you can’t show that you pointed out the requirement.
No one is debating the need for repeat visits when the inevitable Murphy’s Lawkicks in. My feeling is that, by accounting for the predictable problems, you are less impacted by the unpredictable ones.
Click here to read full article on IFSEC Global