With an in-house design, you can’t refuse to renew a service contract if a problem arises later. Planning for any eventuality and designing for easy repair and upgrade become personal goals.
During the construction of Bally’s 1,500-space, self-park garage and skywalk People Mover, our office was asked to design a CCTV system for the structure.
Our staff, in the communications and electronics department at Bally’s Park Place Casino Hotel & Tower, was understandably excited. Although the purpose of this system would be to ensure customer safety, we decided to add some enhancements to the standard design.
Because of the nature of our operation, it’s difficult to discuss specific information on this security system’s size, operation and camera placement techniques. However, from a design and installation point of view, the overall approach and implementation is quite unique and may offer some insight.
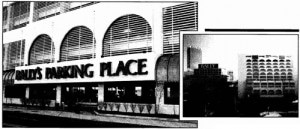
Completed less than a year ago at a cost of more than $28 million, Bally's Parking Place houses more than 1,500 parking spaces.
To appreciate our approach, you have to understand the nature of Bally’s C&E department. Unique among Atlantic City casinos, this department handles virtually all electronics and communications repair and installation throughout the complex. This includes, for example, the maintenance and repairing of more than 1,300 guest room and public area TV sets, troubleshooting data processing lines, repairing 2-way radios and pagers (Bally’s is the only casino in Atlantic City that is a factory-authorized Motorola repair center), performing multimedia and audio setups, and running a broadcast-quality TV production studio.
Thus, our crew of 16 technicians handles a wider range of in-house “clients” than many independent contractors. By far, our most critical job is the installation, repair and maintenance of the CCTV systems. This attention ensures the safety of our guests and patrons and complies with New Jersey’s state gaming regulations.
Before the construction of the parking garage, Bally’s Park Place, like virtually every other casino in Atlantic City, had two independent CCTV systems, one handling security and the other surveillance. Because of the distance involved from the existing security command center to the garage, we decided to construct a completely separate system to handle the new cameras, with tie-lines provided to link the two systems.
In designing this system, we built in the safeguards that had been added to the two other systems over the years to improve reliability. Knowing we would have to repair and upgrade the system over the years, we wanted to make it as serviceable as possible to virtually eliminate downtime.
The Design Phase
In the early stages of designing the system, we decided to write a general specification as to the switch size and performance. Then we’d let various manufacturers tell us what equipment would meet the requirements given to us by the director and assistant director of security. Rather than design a system around the switch, we decided to put the onus on the manufacturers to provide a system that would fulfill the goals of our wish list.
The original design called for some key requirements: expandability to a minimum of 512 inputs by 32 outputs; complete software control of the system from an IBM-compatible PC (to avoid expensive proprietary software upgrades in the future); home-runs to the CPU from each keypad controller (to eliminate the problem — when “daisy-chaining” keypads — of one failure taking the whole system down); the ability of the keypads to function over a cable run longer than 2,000 feet (to provide control functions from the existing command center in the main building); and certain standards of fit, finish and durability
The parking garage is connected to the hotel complex by a glass-enclosed skywalk and People Mover, which transports patrons to the casino level in comfort.
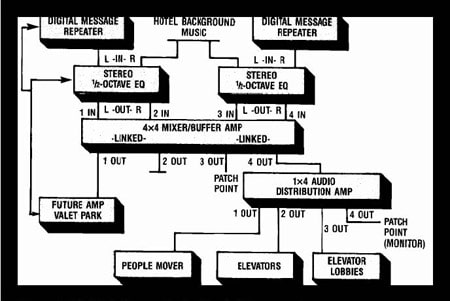
Figure 1. The block diagram for the People Mover sound system
Each potential supplier had to show us an existing system and provide us with full schematics, circuit descriptions and service information. This would allow us to become a repair center for the equipment after the factory warranty had expired. After all, we didn’t want to be a guinea pig for new technology.
While waiting for responses from the manufacturers, we held informal discussions with all of our technicians concerning the nuts-and-bolts parts of the system. We paid particular attention to the wiring and connectors. Samples were ordered and tested extensively for reliability. We wanted to use Belden 9221 mini coaxial cable for certain interconnections within equipment racks to allow better access to the rear of the equipment and to keep the appearance clean. With the high density of connections on the back of the switch and patch panels, using this cable meant the difference between seeing and not seeing the connections.
Our maximum run for this cable would be roughly 25 feet, so we verified and tested it out to 100 feet, leaving an adequate safety margin.
We also researched a multiconductor cable for use in pan/tilt/zoom (PTZ) camera installations to eliminate individual power, control and video cables.
When we settled on Belden 9262, we ordered a 1,000-foot spool to test, again leaving a sufficient safety margin over our maximum 250-foot run for that cable. We didn’t want to know how well something would work on paper. We had the resources of a complete electronics shop at our disposal, so we took full advantage of the situation.
By this time, two manufacturers had responded with systems that would meet our requirements. After going over the technical information provided, seeing their systems in operation and speaking with technical personnel, we chose an American Dynamics switch. The company’s attitude of “no compromises” and our experience with its Select-A-View and other equipment in our existing systems, coupled with the company’s simple and clean design philosophy, helped us finalize our decision.
The basic design of the American Dynamics switch is essentially that of a computer network. The CPU sends data over a single 75: coaxial cable to the input and output bays and accepts RS-232 inputs from keypad controllers and a PC to control system programming. The input and output bays are configured, rather than the individual circuit cards, so that virtually every card is interchangeable. The switch doesn’t require a card to be addressed, so replacement of a bad card in the event of a problem is fast and foolproof.
After we chose the switch and other components in the system, we submitted the entire list of equipment to seven different vendors to ensure a minimum of three bids on each item. We told each vendor that we would purchase on an item-by-item basis, not system-wide, and they were asked to price accordingly.
By varying the types of vendors we contacted, we saved a substantial amount of money without substituting equipment. Vendors also had to be authorized dealers for each item on which they were bidding to avoid problems later with warranty support.
The next hurdle was coordinating the actual installation with two electrical contractors (one running conduit, the other pulling cable) and our two shifts of technicians. Complete installation manuals were produced, including wiring schedules, reduced copies of all of the AutoCAD generated drawings, and rack layouts and elevations. These were distributed daily to the technicians and electricians working on the job.
As the job progressed, each person would mark any changes and revisions in his book. At the end of the project, we collected these books and used them to generate the as-built drawings and reference manual. Because each person’s name was on a book, it was easy to go right to the source if we had questions or needed further clarification.
A local electrical contractor was chosen to run the wiring, and his foreman had experience with camera installations in our main building. He knew what common-sense questions to ask. “I know that pillar is not on the prints, but do you really want your camera behind it?”
By maintaining strong lines of communication, we were able to ensure the optimal placement of cameras and eliminate costly “after the fact” changes. Although everyone wanted some involvement with the system installation, we quickly discovered that the project would have to be broken into smaller jobs and assigned to certain individuals.
All of the subs were allowed some flexibility to complete their jobs without stepping on anyone’s toes. The intent was to instill a sense of pride and accomplishment in each segment of the project, treating each job as if it were the most important (as it was for the person doing it). The actual wiring of the system was handled by our day-shift technicians, with individuals assigned to rack video wiring and power distribution.
Other technicians contributed on a rotating basis to gain familiarity and offer their insights. Because our night crew is smaller and must also handle data processing and TV service calls during the hotel’s busiest hours, they would only be able to work on the system as time and schedule permitted.
Acting as a support team, the night crew performed the difficult task of troubleshooting and debugging cameras as they were installed, allowing technicians working the following day to make the necessary wiring revisions. Having separate teams helped in another unexpected way: When a problem was encountered and one team could not solve it, it was passed on to another.
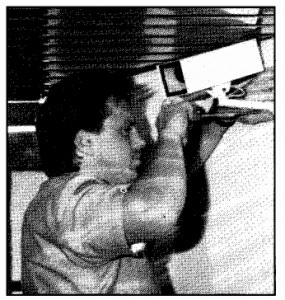
Decorative camera housings were used on the skywalk People Mover
For example, we spent all day trying to figure out why the elevator cameras would intermittently shut off, finally concluding that there was a break in the cable. Before passing the problem to the electrical contrac-tor, we asked the night crew to give it a crack. Using a flashlight and some duct tape, they discovered that there was nothing wrong with the cameras
Attention to Detail
One common problem with equipment racks in this realm is the number and size of cables required for installation and service. Using Winsted racks with 7-inch spacer units between them to serve as cable troths, we gained free access to the back of all equipment for service, more air space for ventilation, and a neater overall appearance.
Patchbays are an important part of a CCTV system, but — unfortunately for the end-user — they are frequently omitted from a system as an unnecessary luxury item. Because all cameras, inputs, key outputs and test points are patchable, virtually any problem can be corrected instantly by simply patching around it.
Servicing is dramatically simplified by eliminating items from the chain until a problem is found, and temporary changes can be made to a system’s configuration to cope with any unforeseen emergency. We chose the Canare patchbay system because of a unique hermetically sealed switch design, a cable tie bar on the back, which makes the installation easier and neater, and its clean, compact appearance.
The system is a mix of fixed and PTZ cameras. Because we had recently upgraded the fixed cameras in the main building from tube to CCD units and had tested about 20 different cameras before deciding on the JVC TKS-210U, we decided to stay with that unit for most of the fixed cameras. We chose the Videolarm VLTL-2 indoor-outdoor enclosure for these cameras. The swing-down design allows you to open the enclosure and adjust the camera without changing the positioning, and it offers the added protection of a weatherproof seal.
Decorative housings were to be used in the elevators and the skywalk People Mover, which connects the garage to the main building. Cameras were carefully selected in conjunction with the enclosures to ensure that picture quality would meet our high standards. Auto-iris units were used on any fixed camera that would be subjected to changing light conditions, and 2-piece cameras were used in the elevators so that picture quality would not be sacrificed for small size.
The PTZ cameras presented a unique problem. In the event that a unit was to fail, the high traffic conditions could make field servicing of the camera difficult. Rather than change camera locations to accommodate servicing, we decided to place the cameras in the optimum locations and make them completely modular, using custom-modified Sensormatic Mini-Domes.
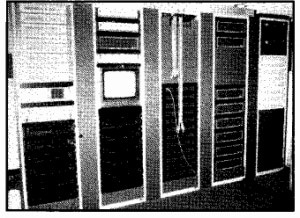
In the equipment racks for the American Dynamics switching system, rack spacers are used to eliminate wiring clutter
Instead of repairing the camera in the field, a technician simply opens the swing-down back-box with a special security tool, unplugs the multipin control and BNC video plugs, removes the camera assembly, which is mounted on a 2′ x 2′ drop-ceiling tile, and replaces it with a spare. The replacement of a camera can be completed in less than two minutes, and the unit can then be taken back to our shop for repair.
The second half of the PTZ equation, the receiver/driver unit, was mounted in an electrical closet on each floor. Rather than use a separate unit for each camera, 8-channel units were purchased, leaving spare receiver channels on each level in case of a failure. A Clear-Corn intercom line was run to each floor from a master station in the command center to allow the technician to speak to the operator when making a repair or adjustment. All video cables (fixed and PTZ cameras) were connected through a BNC barrel connector to allow the technician to break the connection and plug in a battery-powered “Watch-cam” monitor to verify the signal and to make adjustments.
No amount of planning, coordination and experience guarantees perfection. When a large portion of the system was completed, we fired everything up and looked on in anticipation. The switch worked perfectly, the video quality was beautiful, but there were no PTZ functions.
Tearing through service manuals and using all of our diagnostic tools, we looked at every point of the data path, checked connections from rack to receiver to camera, and just about hit every brick wall imaginable. In frustration, we thought about swapping the receiver/drivers in the electrical closets on each floor with spare units, thinking that maybe they had been damaged when they were mounted.
What we found was an extremely low-tech bug: When the weatherproof covers were closed on the cases, the amount of cable in the box pushed the center of the door out just enough so that the service switch would not make contact, shutting off the unit. The moral: In planning for every eventuality, be sure to leave room for Mr. Murphy.
Although this project has involved significant time and resources, the end certainly justifies the means. We’re confident that we can ensure our customers’ safety and enjoyment of our parking garage and the People Mover, regardless of the time of day.